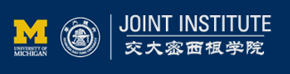
Student Projects
Mars Shelter
Project Video
Team Members
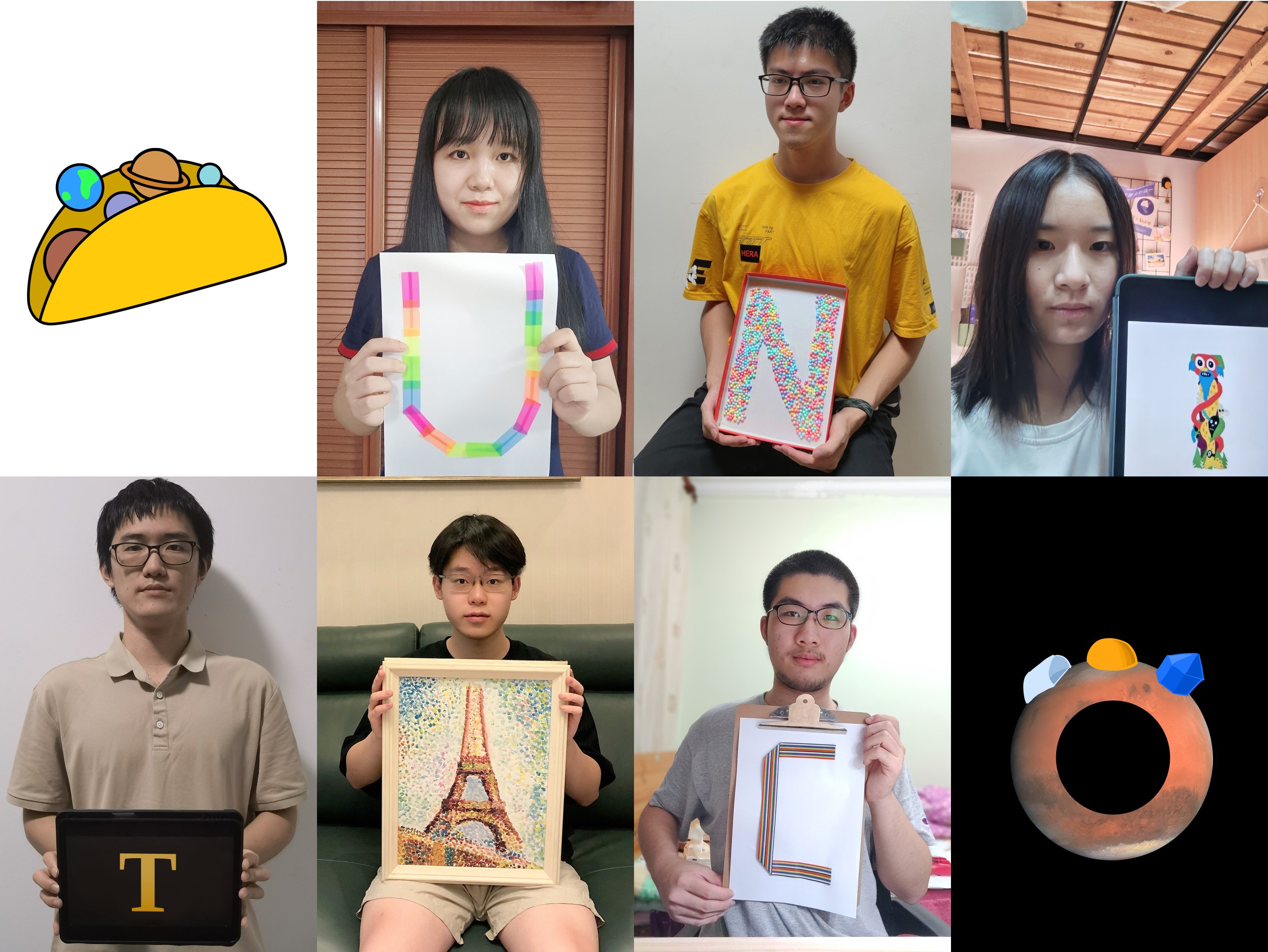
Team Members:
何睿淇 Ruiqi He, 孙诗慧 Shihui Sun, 李闻达 Wenda Li, 尹奕航 Yihang Yin, 何昱树 Yushu He, 杨肇宸 Zhaochen Yang
Instructors:
Yanfeng Shen,Ting Sun
Project Description
-
Problem
This project aims to design a Mars shelter, with the greenhouse as its core, to solve the food shortage in Mars exploration.
To support permanent inhabitancy, a Mars shelter for existence must be accomplished. Among the five major consumables needed for a martian shelter, energy, water, oxygen, construction material are abundant in economic concentrations and extractable forms on the surface of Mars. By contrast, food is not available and cannot easily be created from the raw materials present on Mars. Food, therefore, becomes the core issue for a Mars shelter to tackle with. However, with harsh environmental conditions, growing food locally on Mars will be one of the more challenging in-situ resource utilization process.
-
Concept Generation
To tackle food shortage on Mars, a greenhouse is needed for a shelter to maintain a stable environment and sufficient supply for plantation. The real-time environmental parameters should be monitored and controlled. Currently, the emphasis is put on a monitoring system to track temperature, humidity and brightness. To provide sufficient light for photosynthesis, a light control system that can switch the tint film and LED lights ON/OFF according to the environmental brightness is needed. Another requirement of photosynthesis, water supply, is accomplished by a humidity control system to pump and atomize the proper amount of water into the greenhouse based on the detected humidity.
-
Design Description
Fig. 1 The Overall view of the Mars Shelter
Mechanically, our Mars Shelter is the integration of three co-dependent structures that serve different purposes. Of the three, the Greenhouse is the most critical one. It is a semi-cylindrical structure covered with heat-insulating material. The Pump Station is a hemispherical dome, and the Living District is a hexagonal building for crew residence and miscellaneous facilities.
The mechanical structure we described above hosts our monitor and control system. Hardware-wise, our system consists of four parts: sensors, regulators, microcontrollers and a computer. We use three sensors to monitor the environment inside the Greenhouse: (i) DHT11, a digital temperature and humidity sensor, (ii) the photocell, a light-dependent resistor (LDR), and (iii) a water level sensor [insert working principle here]. In addition to sensing the environment, we also use several other components to regulate the surroundings. These include (i) LED strips for artificial lighting, (ii) a liquid crystal tint film, (iii) a water pump, and (iv) a humidifier. The LEDs are red- and blue-colored, with wavelengths of 630nm and 475nm respectively. Absorption by chlorophyll peaks at these wavelengths[cite reference], which increases efficiency of photosynthesis at night. The opacity of tint film can be toggled depending on the ambient brightness as reported by the LDR. It is clear in the day to allow sunlight to pass through, and opaque at night to optically insulate the Greenhouse from the outside. The water pump is responsible for maintaining the hydration of soil. Water is pumped from a water tank in the Living District to the Greenhouse to irrigate the soil until a certain water level is reached. In the Living District, humidity is maintained using a piezoelectric humidifier which vaporizes a small amount of water into the air.
Two Arduino Uno microcontrollers reside in the Pump Station. One is used to retrieve temperature and humidity from respective sensors, control lighting accordingly (schematics in Fig. 2), and transmit current working status in CSV (Comma-Separated Values) format via USB to the computer, where a Python process parses them and saves them onto the disk. A browser installed on the computer can then be used to visualize recent temperature and humidity values in both radial gauges and line charts, powered by HTML5 and respective JavaScript libraries. We call this visualization interface the Dashboard(Fig. 3). The other Arduino Uno is responsible for water circulation control.
Fig. 2 Schematics of first Arduino board and peripherals thereof. (Generated with KiCad 6.0.6)
Fig. 3 Dashboard as viewed in Firefox.
-
Validation
For the monitoring system, the precision and range of environmental parameters are checked with specifications as follows.
1. The data precision is 0.1℃ for tempereture and 1% for humidity.
2. The detected range cover temperature from -20℃ to 60℃ and humidity from 5% to 95%.
Below specification of energy consumption can be met in light control system.
1. The power of the red LED strip is 1.2W and 0.4W for the blue ones.
2. The tint film requires 2 to 4 times less energy than the jalousie.
For the humidity control system, the energy efficiency, water volume and materials are checked.
1. The humidifier’s drive chip will automatically shut down after 4 hours of continuous work.
2. The system could operate under 2W at 108 kHz.
3. The water pump comes with 1.2KG water pressure, 25cm suction and 20cm lift, which guarantees the normal irrigation.
-
Modeling and Analysis
The data is visualized in a web browser, making it compatible for device upgrades, customizable, and perceivable. They also feature high precision and wide range.
Fig. 4 Dashboard
The light wavelengths of the LED are optimized to red and blue according to the absorption spectrogram. Absorption by chlorophyll peaks at these wavelengths will increase efficiency of photosynthesis at night.
Fig. 5 Absorption Spectrogram[1]
Automatic and eco-friendly water pump, humidifier and tensiometer are installed to automate the humidity control process. As the water soaks the entire tensiometer, the system will cut off power supply automatically and enter the sleeping mode.
Fig. 6 The Humidity Control System
-
Conclusion
The Mar Shelter smoothly performs multi-functions including humidity, temperature and light density monitoring, humidity and light density control in ultimate tests. It provides a primary pattern of the Mars shelter, which could be a reference for improving chances of survival during the colonization of Mars since it guaranteed the basic needs, especially food supply in a sustainable way.
The Mar Shelter highlights the data visualization, the high precision of the monitoring, and the automatic control system. The environmental data collected are concentratedly displayed on a dashboard to give real-time feedback, which ensures the residents are clear about the conditions at any time. Besides, the high precision guarantees the validity of the data, and the automatic control not only improves the safety of residents but also reduces people’s workload. Moreover, the prototype is mostly made of common discarded goods, which are cheap and environmentally friendly. However, due to technical limitations, the plan for temperature design is abandoned. Also, since the quality of red LEDs and blue LEDs is not considered carefully, the red LEDs do not perform fully in the final results.
The project progress matched the original plan with reasonable resource distribution. In retrospect, design and tests in parts increase the efficiency and are necessary to ensure every function is ready for the final assembly. The circuit control throughout the whole project contributes the most to implementing the functions; further consideration for hiding wiring and improving the voltage distribution in real-life conditions.
-
Acknowledgement
Professor Yanfeng Shen, UM-SJTU Joint Institute
Professor Ting Sun, UM-SJTU Joint Institute
Hao Zhang, Haojia Sun, Xiaoyan Bai and Yi Liang, VG100 Teaching Assistants at UM-SJTU Joint Institute
-
Reference
[1] Hillier, W., and Babcock, G. T., “Photosynthetic Reaction Centers,” Plant Physiology, vol. 125, 2001, pp. 33–37.